Electrolyte Gel Model: Experimentation
1. Purpose
The developed model of the polymer gel needs to be verified through matching
of the computer simulation results to the experimentation results. Our goal is
to design and construct the appropriate experimental setup to test and verify
the electrolyte polymer gel's lumped parameter model. In addition, the
experimental setup will be employed to test simple control strategy in
controlling the gel.
2. Requirements
- The length/volume of the gel must be measured.
- The force/tension applied to the gel must be measured or inferred.
- The uniformity of the surrounding bath's condition must be achieved at
much faster rate than the gel's dynamics.
- The pH and the ion concentrations of the surrounding bath should be
accurately controlled and monitored.
In addition, the desired characteristics of the experimental setup are as
follows.
- Fluid volume usage should be as low as possible.
- The hydrodynamic effect on gel should be minimum.
- Fluid leakage to surrounding should be kept relatively low.
- The effect of friction should be minimum.
- The gel should be visible.
- The data acquisition should be computer controlled for precision.
3. Proposed Designs
3.1 Design No. 1
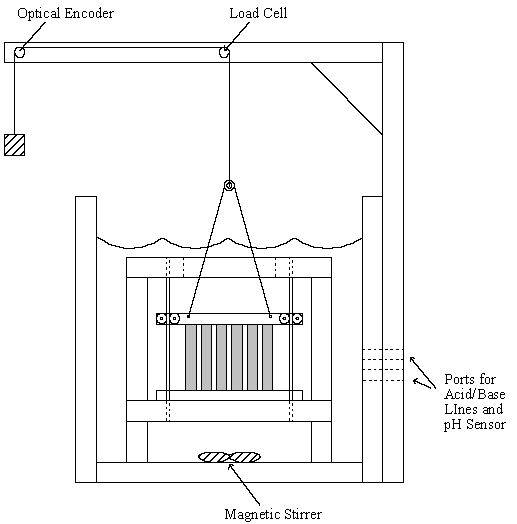
In this design, the strips of the polymer gel sheet are mounted on a common
block which slides vertically on two rails. The whole gel/slider assembly is
immersed in the bath of the surrounding solution, and the gel is activated by
changing the pH of the bath solution. The contracting and expanding gel raises
and lowers the weight, and the length of the gel and the force applied to the
gel are measured by the optical encoder and the load cell respectively. The
magnetic stirrer situated at the bottom of the bath enhances the uniformity of
the bath condition. Following are the pros and the cons of this design.
Pros:
- Planar configuration of gel in sheet form greatly increase surface area
of gels and therefore induces faster response.
- Multiple units can be easily incorporated, and the number of units can
be varied to meet the desired load.
- Gel film thickness can be easily varied.
- Gel unit termination is simple.
- There is no leakage of fluid to environment.
- The gel units are visible.
- The uniformity of the bath solution's condition is quickly achieved due
to active stirring.
- The length and the force are easily measured.
Cons:
- Lateral expansion/contraction may induce undesirable stress on
gel at near the termination.
- Employing multiple gel units may induce uneven swelling.
- The apparatus is bulky.
- Hydrodynamic force on the outer gel units may be significant due to
stirring.
- Change in thickness of film will be difficult to observe.
- The source fluid usage is relatively high due to relatively large volume
of the bath.
- Cycling of the bath pH without flushing out the bath solution would
undesirably increase the ion (salt) concentration of the bath. Flushing the
bath solution would be a slow process.
- The friction at the sliding joints and the pulleys may have significant
effect on the gel performance.
3.2 Design No. 2
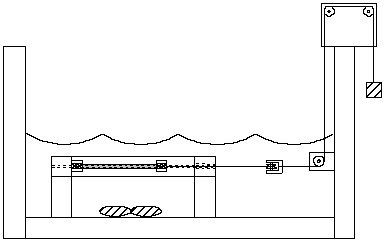
This design is similar to the design no. 1 (planar design) except the gel
units are situated horizontally rather than vertically. As a result, the
hydrodynamic disturbance force due to stirring would be significantly reduced.
However, this design employees an extra pulley, and thus would increase the
overall friction. Rest of the design characteristics are identical to the
design no. 1.
3.3 Design No. 3
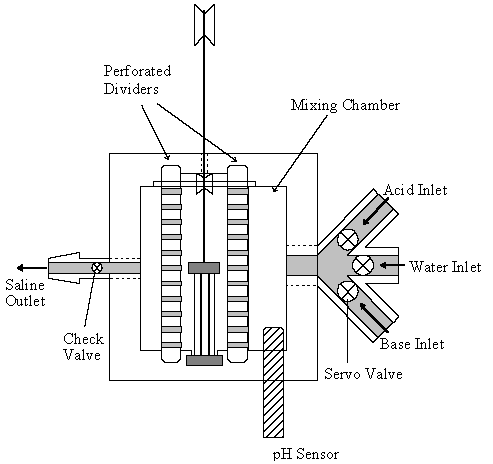
Top View
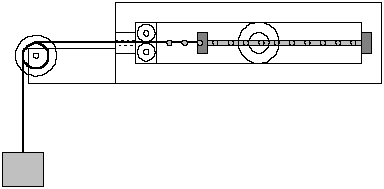
Side View
Unlike the previous designs, in this design, a single gel strip unit is
situated in a relatively small enclosed chamber. The internal chamber is
further divided into three chambers separated by perforated dividers. The
acid/base solutions and the water flows into the first chamber where the mixing
occurs, and the mixed solution would then diffuse into the middle chamber where
the gel unit is situated and to the outlet chamber. The separate acid, base
and water inlet flows are controlled by either servo valves or flowrate
controlled pumps located at just the upstream of the inlet ports. The pH sensor
continually monitors the pH level in the mixing chamber, and the appropriate
amount of acid/base/water will be injected into the mixing chamber based on pH
measurement and theoretical calculation.
Pros:
- The apparatus is relatively compact.
- he frictional effect would be small since it requires only one
pulley.
- Employees planar configuration of gel for short diffusion time.
- The flow direction is perpendicular to the gel orientation, and if the
width of the gel is relatively small, the hydrodynamic disturbance would be
minimal.
- The check valve located at the outlet port prevents the back flow of
saline solution into the internal chamber. In addition, since small pressure
differential is required to induce flow through the check valve, it allows to
inject only the necessary amount of source acid/base/water fluid to achieve
desired internal pH and maintain constant pH level inside without continuos
flow. Such strategy will significantly reduce the volume of the fluid used.
- Cycling of the internal pH can be easily achieved by simply flushing the
internal saline solution with water and injecting appropriate amount of the
source fluid since the volume of the internal chamber is small.
- The gel units are visible.
- Leakage of fluid to environment would be small.
- The length and the force are easily measured.
Cons:
- Since there is no active mixing device, the diffusion process of
solution through the perforated dividers into the middle/outlet chambers may be
slow. The internal chamber volume should be minimized to minimize the
diffusion time.
- Delivery of accurate amount of source fluid into the internal chamber
may be difficult. In addition, since the internal chamber volume is small, the
error in the internal pH would be more sensitive to the accuracy of the source
fluid delivery in comparison to the previous designs.
3.4 Design No. 4: Enhancement of Design No. 3
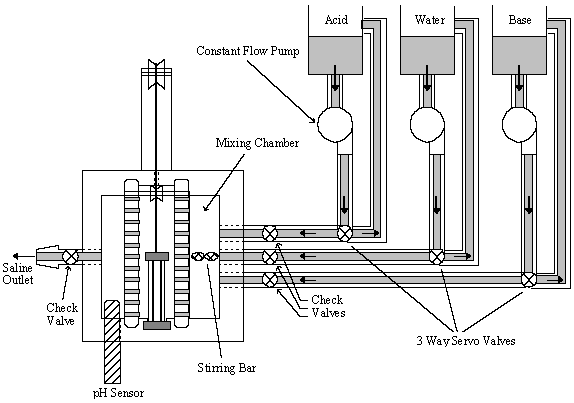
This design attempts to address the potential difficulties the design no. 3
faces, and the enhancements are as follows.
- The check valves at the inlet and outlet of the chambers help retain the
fluid inside without continuous flow.
- Active stirring employing the miniature stirring bar would greatly
enhance the overall mixing process while the perforated wall between chambers
will minimize the hydrodynamic disturbances the gel experiences.
- The constant flow pump (peristaltic pump) with 3 way servo valves should
allow relatively precise delivery of the source fluids into the chamber. When
the valve is closed, the pump will simply circulate the fluid back into the
reservoir whereas when the valve is open, the flow is channeled into the
chamber while maintaining preset constant flowrate.
- Capability to inject precise amount of fluid would reduce dependency on
"relatively slow" pH sensor in overall control system.
This design is selected for the gel model verification test setup, and the
detailed diagram of the design is shown below. As shown below, the
terminations of the gel strip will be molded into the epoxy blocks along with
the transmission cable.
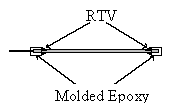
Schematic of the gel model testing device.
4. Experimentation
Primary goal of the experimentation would be to test the effects of the
surrounding bath pH, ion concentrations and the mechanical loading on the gel's
static and dynamic swelling behavior. Especially, the change in gel's swelling
in response to change in the mechanical loading is of particular interest. The
PVA/PAA gel is proposed for this purpose rather than the PAN gel because the
model is suitable for unipolar gel only at this point. The PAN gel exhibits
severe discontinuous hysterisis, i.e. it swells at high pH and contracts at low
pH due to its bipolar nature. On the other hand, the unipolar PVA/PAA exhibits
continuous non-hysteric response at near the neutral pH. The mechanical
strength and the response speed of the PVA/PAA gel fall much short of the PAN
gel fiber. However, for our purpose, the performance is of major concern.
The experimental results will be compared to the computer simulation results
based on the theoretical lumped parameter model, and the model will be further
enhanced. Upon successful verification of the model, a simple control strategy
will be implemented.